How to Make a Patterned End Grain Cutting Board
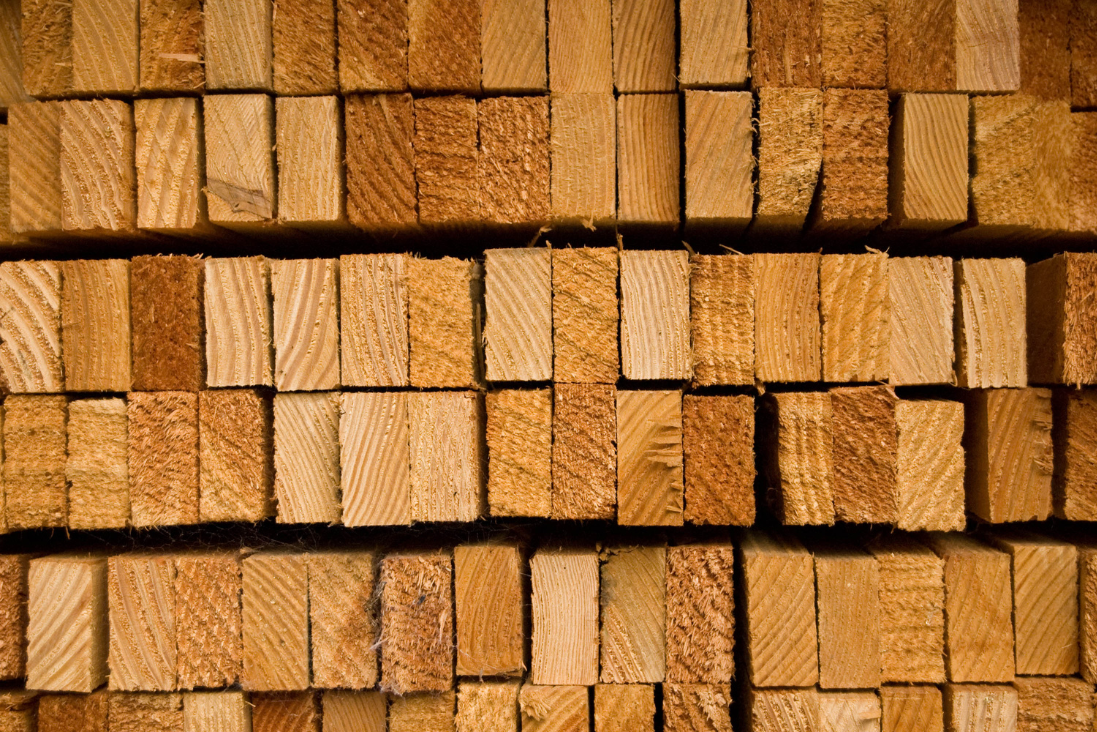
If you’ve ever spent time in the kitchen, you know the value of a good cutting board. But there’s something special about an end grain cutting board. Not only are they incredibly durable, but they also add a touch of craftsmanship to your kitchen that a mass-produced board simply can’t match. If you’ve been thinking about making one yourself, you’re in the right place. Creating an end grain cutting board isn’t the simplest woodworking project out there, but with some patience and attention to detail, it’s absolutely within reach—even if you’re not a seasoned pro.
Related: Best Cutting Boards
Unlike a traditional face grain or edge grain cutting board, where the knife cuts along the wood fibers, an end grain board has the fibers oriented vertically. This means your knife cuts into the fibers rather than across them, which makes the board more durable and gentler on your knives. When you make a cut, the fibers part slightly, then spring back into place, which helps the board resist showing cuts and keeps your blades sharper for longer.
Materials Needed
- Hardwood lumber: Nine boards with a 1-1.5 inch thickness, at least 27 inches long. The width of the boards can vary, but commonly used widths are around 4 to 6 inches.
- Wood glue
- Mineral oil
- Beeswax (optional)
- 4 rubber feet with screws (optional)
Tools Needed
- Table saw
- Jointer
- Planer
- Drum sander or belt sander
- Random orbital sander
- 6-8 large clamps
- Cauls
- Router with round-over bit
- Miter gauge or crosscut sled
- Flattening sled (optional)
- Digital angle finder
- Tape measure or ruler
- Square
- Hand plane or router sled
- Brush or foam applicator
Related: Best Charcuterie Boards
How to Make an End Grain Cutting Board
Step 1: Preparing Your Wood
The first step in creating an end grain cutting board is selecting the right wood. You’ll want to use hardwoods with tight grains, like maple, walnut, or cherry. These woods are durable, resist moisture, and stand up well to daily use. If you’re feeling adventurous, you can mix and match woods to create a striking pattern. Just keep in mind that combining different species will require careful attention to ensure that all the pieces work well together in terms of both aesthetics and performance.
Start by milling your lumber to get flat, straight boards. If you’re starting with rough lumber, this means using a jointer to flatten one face, then planing the opposite face to create parallel surfaces. After that, rip the boards to the desired width on the table saw. Typically, you’ll want your strips to be about 1 to 1.5 inches wide. It’s crucial that these pieces are consistent in width because any variation will show up later when you’re assembling the board.
Step 2: Gluing the Strips
Once your strips are cut, it’s time for the first glue-up. Arrange the strips in the pattern you want, making sure the end grain of each piece will be facing up in the final board. This initial glue-up will look just like a long grain cutting board, but don’t worry—we’re only halfway there.
Apply a generous amount of waterproof wood glue (such as Titebond III) to each joint, then clamp the assembly tightly. You want to see glue squeeze out along the seams, which indicates you’ve used enough glue. If any of the strips shift out of alignment during clamping, gently adjust them. It’s important to get this first glue-up as flat as possible to minimize the amount of work you’ll need to do later.
Let the glue cure fully—usually overnight—before moving on to the next step.
Step 3: Cutting and Reassembling
Once your glue is dry, it’s time to turn that long grain board into an end grain cutting board. Start by cleaning up one edge of the glued-up panel using a table saw or jointer, then cut the panel into equal-width strips. These strips will now be your building blocks for the final board, with each strip’s end grain facing up.
Here’s where the magic happens: flip every other strip end over end. This simple flip creates the classic checkerboard pattern that end grain cutting boards are known for. If you want to get a bit more creative, you can experiment with flipping strips in different ways to create various patterns. The key is consistency—make sure all the strips are aligned perfectly before moving on to the next glue-up.
Step 4: The Final Glue-Up
This next step can be a bit tricky, so take your time. You’ll want to repeat the gluing process, but this time with the strips oriented so that the end grain is facing up. Once again, apply a generous amount of glue and clamp the strips tightly together. End grain boards can be prone to shifting under pressure, so consider using cauls (straight pieces of wood clamped across the board) to keep everything aligned as the glue dries.
Because end grain cutting boards tend to absorb more glue than face or edge grain boards, you might notice some gaps or unevenness after the glue has dried. Don’t panic—this is normal and can be fixed in the next step.
Step 5: Flattening and Sanding
Once the final glue-up is dry, you’ll likely have a board that’s not perfectly flat. Flattening an end grain board requires some care, as end grain is more prone to tear-out when using power tools. If you have access to a drum sander, this is the perfect tool for the job. If not, you can use a planer, but be sure to take very light passes and make sure your blades are sharp. Some woodworkers prefer to use a hand plane or a router sled for this step, which gives you more control but requires more time.
After flattening, move on to sanding. Start with a coarse grit (around 80) to remove any remaining high spots or glue, then work your way up to finer grits (120, 220, and even 320) to achieve a smooth, polished surface. Pay special attention to the edges of the board, and consider adding a slight chamfer or round-over with a router to soften the corners and prevent chipping.
Finishing Touches
The final step in making your end grain cutting board is applying a finish. Since this is a kitchen item, you’ll want to use a food-safe finish, like mineral oil or a mixture of mineral oil and beeswax. Apply the finish liberally, allowing it to soak into the end grain. Because end grain is so absorbent, you may need to apply several coats, allowing each one to soak in before applying the next.
After the oil has had time to penetrate, wipe off any excess and let the board dry. If you like, you can buff the board with a soft cloth to bring out a bit of sheen.
Our Recipe for Trust: Why Choose Kitchen Institute
At the Kitchen Institute, we're dedicated to providing reliable and accurate information on cooking trends, tips, and product reviews. Our team of passionate food enthusiasts ensures that every piece of content is thoroughly researched and based on real-world experience. We pride ourselves on our comprehensive and unbiased product reviews, rigorous research processes, and commitment to staying current with the latest culinary innovations. Trust us to enhance your culinary journey with quality insights and practical advice.